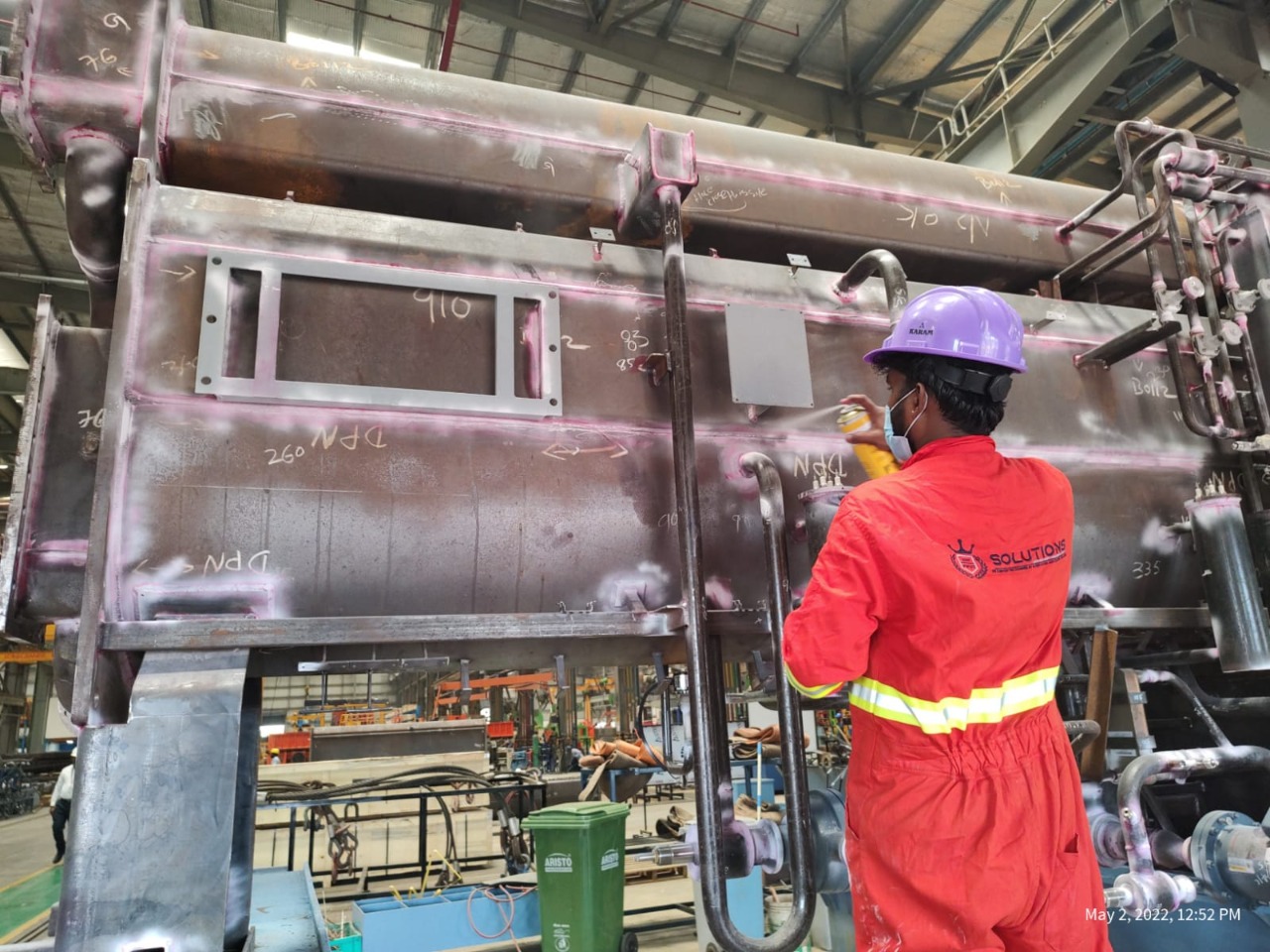
Liquid Penetrant Inspection (LPI / Dye Penetrant Inspection (DPI)
Liquid Penetrant Inspection (LPI / Dye Penetrant Inspection (DPI)
Introduction:
Liquid Penetrant Inspection (LPI), also known as Dye Penetrant Inspection (DPI), is a widely used non-destructive testing (NDT) technique in various industries to detect surface defects in materials. It is a reliable and cost-effective method that involves the application of a liquid penetrant to the test surface, followed by the removal of excess penetrant and the application of a developer to make the defects visible. In the NDT industry, NDT and PWHT Solutions have emerged as a leading company, offering exceptional LPI services that set them apart from their competitors. This article explores the significance of LPI and highlights the unique aspects of NDT and PWHT Solutions’ service offerings.
The Significance of Liquid Penetrant Inspection (LPI):
Liquid Penetrant Inspection plays a crucial role in the NDT industry as it allows for the detection of surface-breaking defects such as cracks, porosity, leaks, and other discontinuities that are not readily visible to the naked eye. By employing LPI, companies can ensure the integrity and reliability of critical components and structures, thus preventing potential failures and ensuring the safety of personnel and the public. Industries such as aerospace, automotive, manufacturing, petrochemical, and power generation heavily rely on LPI to assess the quality and condition of their products.
NDT and PWHT Solutions: Delivering Exceptional LPI Services:
NDT and PWHT Solutions have established themselves as a reputable company that excels in delivering high-quality Liquid Penetrant Inspection (LPI) services. Their commitment to excellence and customer satisfaction sets them apart from their competitors. Here are some key aspects that make NDT and PWHT Solutions unique in providing LPI services:
Industry Expertise:
NDT and PWHT Solutions boast a team of highly skilled and certified technicians with extensive experience in the NDT industry. Their experts possess in-depth knowledge of LPI techniques, industry standards, and specifications. This expertise enables them to effectively identify, evaluate, and interpret indications, providing clients with accurate and reliable inspection results.
State-of-the-Art Equipment:
To ensure the highest level of precision and accuracy, NDT and PWHT Solutions invest in advanced equipment and technologies for their LPI services. They utilize cutting-edge penetrant materials, developers, and inspection equipment, which significantly enhance the sensitivity and detection capabilities of the inspection process. By staying up-to-date with the latest advancements in NDT equipment, they can deliver superior results to their clients.
Customized Solutions:
NDT and PWHT Solutions understand that each client’s requirements are unique. Therefore, they offer tailored LPI solutions to meet specific needs. Whether it is on-site inspections, in-house testing, or emergency response, they design their services to accommodate diverse industrial settings, project timelines, and budgets. Their flexibility in providing customized solutions ensures optimal inspection outcomes for every client.
Stringent Quality Assurance:
Maintaining the highest standards of quality is a top priority for NDT and PWHT Solutions. They have implemented rigorous quality assurance practices at every stage of their LPI services. From initial preparation and application of penetrant to the final evaluation of results, their processes adhere to industry standards such as ASTM E1417 and ISO 3452. This commitment to quality ensures accurate defect detection and provides clients with confidence in the integrity of their products.
Timely Reporting and Documentation:
NDT and PWHT Solutions recognize the importance of timely reporting and documentation. Upon completion of LPI inspections, they provide comprehensive and detailed reports to their clients, outlining the findings, analysis, and recommendations. The reports are prepared with clarity and precision, enabling clients to make informed decisions promptly. This efficient reporting system sets them apart from their competitors and ensures a seamless experience for their clients.
Conclusion:
Liquid Penetrant Inspection (LPI) is a vital NDT technique used to identify surface defects in various industries. NDT and PWHT Solutions have established themselves as a trusted provider of LPI services, offering unmatched expertise, advanced equipment, customized solutions, stringent quality assurance, and efficient reporting. Their commitment to delivering exceptional services sets them apart from their competitors, making them the go-to choice for industries seeking reliable and accurate LPI solutions. By choosing NDT and PWHT Solutions, companies can ensure the integrity and safety of their products while benefiting from their industry-leading expertise and customer-centric approach.
Liquid Penetrant Inspection (LPI), also known as Dye Penetrant Inspection (DPI), is a widely used non-destructive testing (NDT) technique in various industries. It offers several benefits, including:
Surface Defect Detection: LPI/DPI is highly effective in detecting surface-breaking defects, such as cracks, fractures, porosity, laps, and seams. It can identify flaws that are not visible to the naked eye, ensuring the integrity of the inspected component.
Versatility: LPI/DPI can be applied to a wide range of materials, including metals, plastics, ceramics, composites, and even non-porous materials. This versatility makes it suitable for diverse industries, such as aerospace, automotive, manufacturing, and oil and gas.
Cost-Effectiveness: Compared to other NDT methods like radiography or ultrasonic testing, LPI/DPI is relatively inexpensive. The equipment and consumables required are affordable, making it a cost-effective option for routine inspections and quality control processes.
Quick Inspection: LPI/DPI provides rapid results as the inspection process is relatively simple and straightforward. The application of the penetrant, dwell time, and the removal of excess penetrant are usually quick, allowing for efficient inspection and faster turnaround times.
High Sensitivity: The penetrant used in LPI/DPI is designed to have excellent capillary action, allowing it to penetrate even the smallest surface defects. This high sensitivity ensures that even minute cracks or flaws are detected, enhancing the overall quality control process.
Ease of Application: LPI/DPI is a relatively easy technique to implement. It does not require extensive training or specialized equipment, and the process can be carried out in various environmental conditions. This ease of application makes it accessible to a wide range of operators and industries.
Portable and Field Applicable: LPI/DPI can be performed on-site, making it suitable for field inspections. Portable kits are available, enabling inspections to be conducted in remote locations, eliminating the need to transport large components to a testing facility.
Enhanced Safety: LPI/DPI is a non-hazardous method that does not involve ionizing radiation or emit harmful emissions. This aspect ensures the safety of operators and the environment during the inspection process.
Defect Localization: LPI/DPI can provide precise information about the location and extent of surface defects. This data assists in determining the severity of the flaws and aids in subsequent repair or maintenance decisions.
Quality Assurance: LPI/DPI helps ensure the quality and reliability of components, preventing failures and accidents that could arise from undetected surface defects. It is an integral part of quality assurance programs and helps maintain the integrity of critical structures and equipment.
It is worth noting that LPI/DPI has its limitations and may not be suitable for all types of defects or materials. However, when applied correctly, it is an effective and widely used technique in the NDT industry, providing valuable information for quality control and safety assurance.
to detect any surface-connected discontinuities such as cracks from fatigue, quenching, and grinding, as well as fractures, porosity, incomplete fusion, and flaws in joints.
For More Information Contact Our Expert Team: support@solutionss.org