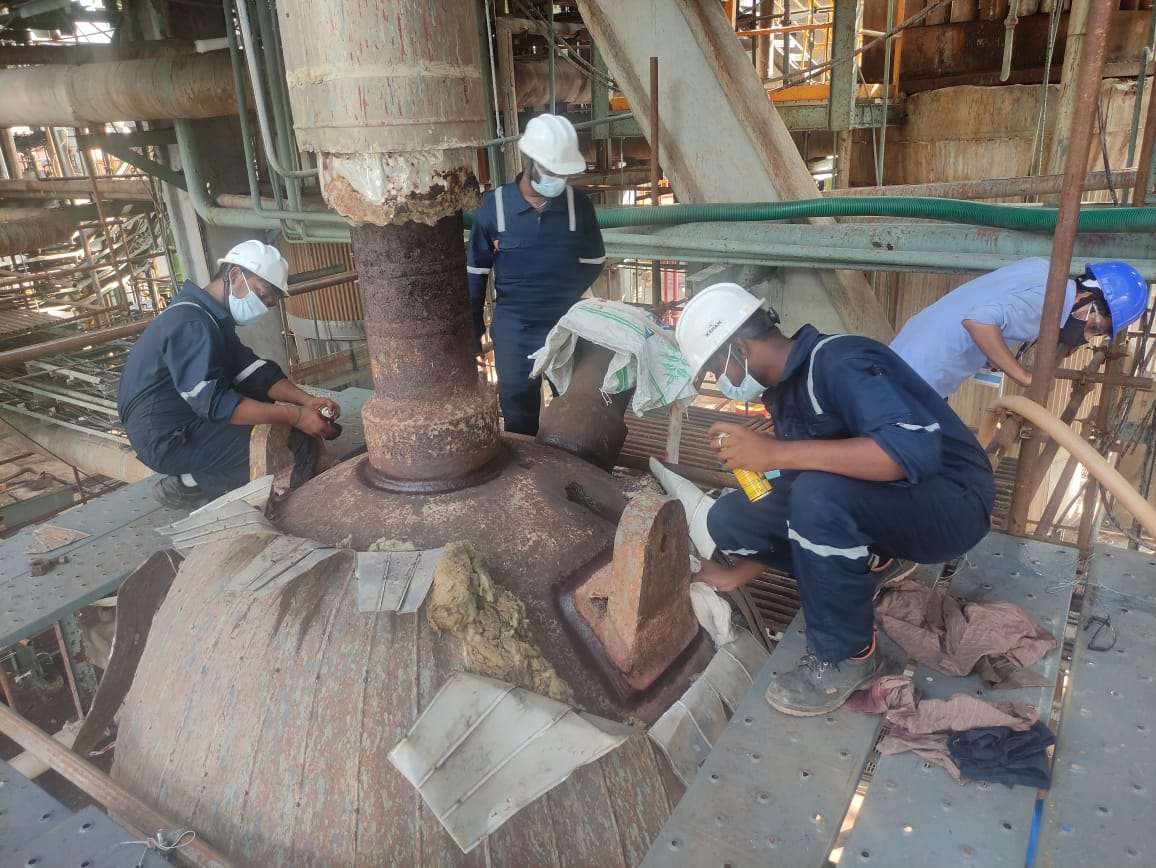
HIGH TEMPERATURE PHASED ARRAY ULTRASONIC TESTING (PAUT)
HIGH TEMPERATURE PHASED ARRAY ULTRASONIC TESTING (PAUT)
Advanced non-destructive testing (NDT) methods like phased array ultrasonic testing (PAUT) use ultrasonic waves to find and characterize interior flaws in materials like metals, composites, polymers, and ceramics. PAUT is widely utilized in a variety of sectors, including manufacturing, power production, oil & gas, and aerospace. In PAUT, an inspection probe made up of numerous separate transducer components is employed to deliver ultrasonic waves into the substance under consideration. The ability to independently control each transducer component enables real-time focusing and direction changes for the ultrasonic beam. The same receiving probe or a different receiving probe is used to detect the reflected waves, and the data is analyzed with specialized software to produce a visual representation of the material’s interior structure. In comparison to conventional ultrasonic testing methods, the utilization of several transducer elements and the ability to alter the direction and focus of the ultrasonic beam enable more accurate and effective inspections. Additionally, PAUT can be utilized to examine parts with complex geometries and atypical shapes. In a number of materials, including metals, composites, polymers, and ceramics, PAUT is frequently used to find flaws such as cracks, voids, inclusions, and delaminations. The method can also be used to gauge a material’s thickness and spot changes in characteristics like density and flexibility.
PAUT is an effective instrument for material inspection and internal problem detection. It is a useful technique for verifying the safety and dependability of crucial components in numerous sectors because of its adaptability and accuracy. In comparison to other conventional ultrasonic testing techniques, phased array ultrasonic testing (PAUT) is a potent non-destructive testing approach with several benefits. There are, however, some restrictions and possible downsides to take into account. Here are some PAUT benefits and drawbacks:
Because PAUT can focus and guide the ultrasonic beam, it can produce findings that are more exact and accurate than those obtained by conventional ultrasonic testing techniques.
PAUT can quickly inspect a vast area, cutting down on inspection time and increasing effectiveness.
PAUT is capable of detecting a range of flaws, including cracks, voids, inclusions, and delaminations, and may be used to check a variety of materials, including metals, composites, plastics, and ceramics.
PAUT can conduct a thorough interior examination of the substance being tested to find subsurface flaws.
PAUT is suitable for automated inspections and remote operations, making it the best choice for inspections in risky or challenging areas.
Compared to certain other non-destructive testing techniques, PAUT is a more complicated and expensive approach that requires specialised equipment and skilled personnel to execute properly.
For accurate inspections, PAUT requires a clean, smooth surface, which could take more time and resources to prepare.
PAUT’s limited penetrating powers make it unsuitable for evaluating thicker or more complicated materials.
Specialized probes or cooling techniques may be needed if standard PAUT probes are insufficient to inspect materials at high temperatures.
If the PAUT is not calibrated correctly or if there is an operator mistake, it may create false positives, which could necessitate unnecessary repairs or component replacement.
In general, PAUT is a strong and adaptable method that may deliver precise and thorough inspection results, but it necessitates specialized tools, skilled labor, and careful evaluation of its constraints and potential downsides.
When inspecting materials at high temperatures, which are typically between 200°C and 600°C, high-temperature PAUT is utilized. This method is very helpful for examining materials in high-temperature applications, such as pipelines, boilers, and gas turbine parts. Several industries that work with high-temperature materials can use this technology, such as:
In power plants, essential components including turbine blades, steam pipes, and boiler tubes are inspected using high-temperature PAUT. This makes sure the equipment functions safely and effectively by making it easier to spot flaws like cracks and rust.
In the oil and gas business, high-temperature PAUT is used to inspect pipelines, pressure vessels, and other equipment. This improves the capacity to spot flaws like corrosion and weld flaws, hence maintaining the equipment’s dependability and safety.
Heat exchangers, exhaust systems, and turbine blades are among the components that are inspected using high-temperature PAUT. This ensures that the equipment functions safely and effectively by making it easier to spot flaws like cracks, corrosion, and erosion.
During the manufacturing process, materials and components are inspected using high-temperature PAUT. This ensures the final product’s quality and dependability by making it easier to find flaws like voids and inclusions.
In order to better understand the behavior of materials at high temperatures, researchers and developers employ high-temperature PAUT. This advances our knowledge of how materials respond to harsh circumstances and may pave the way for the creation of novel materials and technologies.
A phased array probe is utilized in High-Temperature PAUT to send ultrasonic waves into the material being examined. The probe is made up of numerous separate transducer components that may each be manipulated separately, enabling real-time focusing and direction changes for the ultrasonic beam. The same receiving probe or a different receiving probe is used to detect the reflected waves, and the data is analyzed with specialized software to produce a visual representation of the material’s interior structure. The requirement to shield the probe and the connected electronics from the intense heat is one of the main difficulties in high-temperature PAUT. Air-cooled probes, water-cooled probes, or probes with specialized coatings are frequently used to accomplish this. A careful management of the inspection procedure is also necessary to prevent thermal shock and guarantee that the material under inspection does not reach its maximum operating temperature. High-Temperature PAUT has a number of key benefits, including:
Defects are accurately detected by PAUT using sophisticated algorithms to analyze ultrasonic data, which results in the reliable and accurate identification of flaws like erosion, corrosion, and cracks.
PAUT can inspect huge areas fast and effectively, cutting down on inspection time and boosting output.
PAUT is a safe and economical inspection approach because it is a non-destructive testing method that does not harm the material being inspected.
Metals, composites, and ceramics are just a few of the many materials that PAUT can be used to inspect.
High Temperature PAUT is a potent tool for material inspection in high-temperature situations overall. It can assist in preventing catastrophic failures and extending the lifespan of important components by identifying and characterizing internal flaws. As more uses are found for the technology and as it advances, the scope of High Temperature PAUT is constantly growing. The need for dependable and precise inspection methods like PAUT is projected to increase as long as companies continue to use high-temperature materials.
We conduct a wide range of NDT services for your industrial equipment including in-service high-temperature testing to identify and monitor defects.
For More Information Contact Our Expert Team: support@solutionss.org