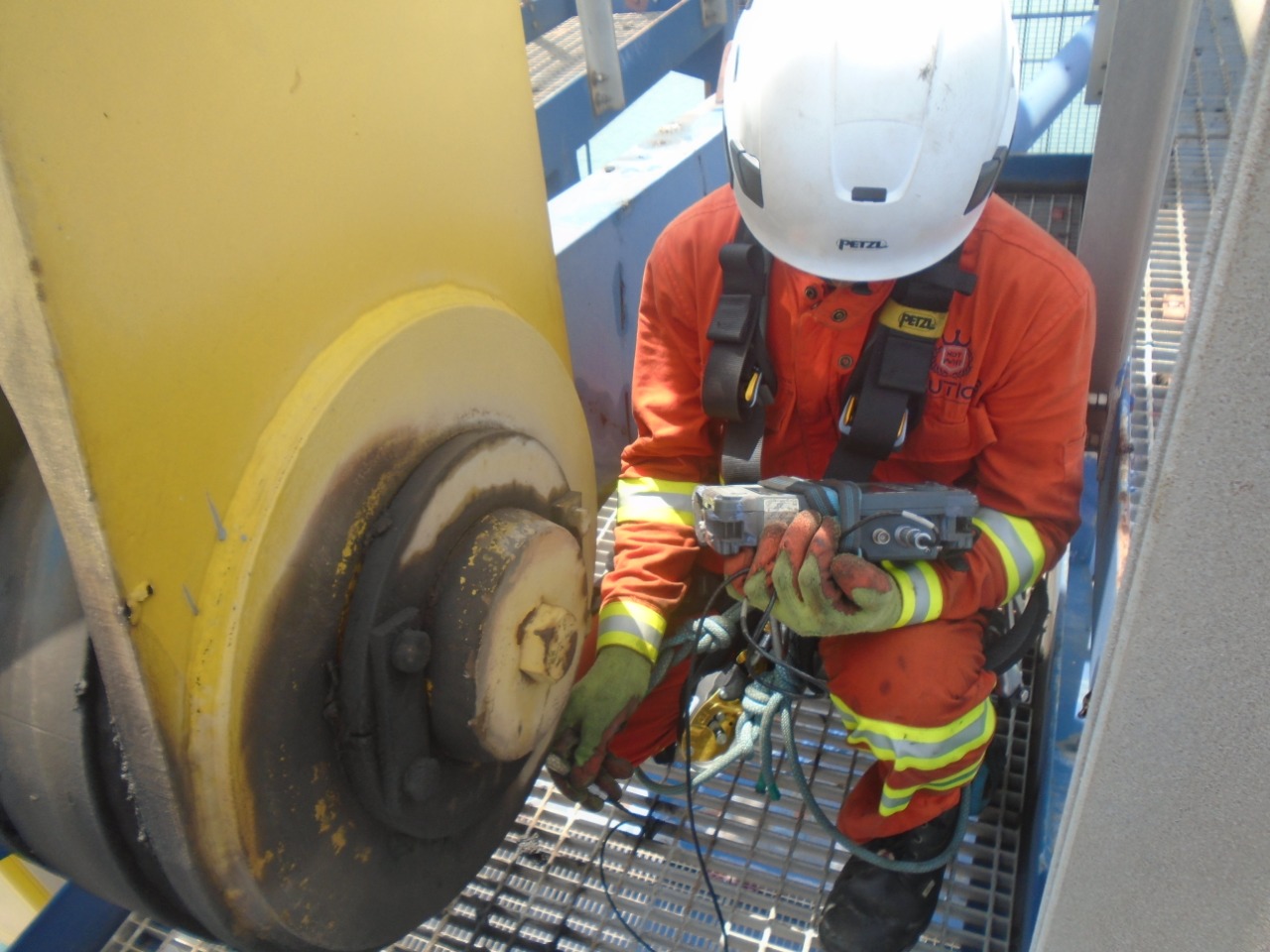
Eddy Current Inspection (ECI)
Eddy Current Inspection (ECI)
Introduction:
Eddy Current Inspection (ECI) is a widely employed non-destructive testing (NDT) technique that plays a critical role in ensuring the structural integrity and quality control of various materials and components. In the NDT industry, NDT & PWHT Solutions has emerged as a leading provider of ECI services, renowned for its expertise, exceptional customer service, and unique approach. This article aims to provide an in-depth understanding of ECI and highlight how NDT & PWHT Solutions excels in delivering these services, setting itself apart from competitors.
Eddy Current Inspection (ECI):
Eddy Current Inspection is a non-destructive testing method that utilizes electromagnetic induction to detect surface and subsurface defects in conductive materials. It is particularly effective in evaluating the integrity of components made from metals such as aluminum, copper, and steel. ECI works by inducing alternating current (AC) into a probe or coil, creating a magnetic field that interacts with the material under examination. Any irregularities or defects in the material’s electrical conductivity or magnetic permeability generate eddy currents, which induce changes in the probe’s electrical properties. These changes are then measured and analyzed to identify potential flaws.
Applications of Eddy Current Inspection:
ECI finds widespread applications across various industries, including aerospace, automotive, power generation, manufacturing, and oil and gas. It is commonly employed for inspecting welds, detecting cracks, measuring material thickness, identifying corrosion, verifying heat treatment, and assessing the quality of electrical conductors. The versatility and efficiency of ECI make it an indispensable tool for ensuring the safety, reliability, and regulatory compliance of critical components.
NDT & PWHT Solutions: Leaders in Eddy Current Inspection Services
Expertise and Experience:
NDT & PWHT Solutions boasts a team of highly skilled technicians and engineers with extensive expertise in ECI. They possess in-depth knowledge of ECI techniques, equipment, and data analysis, enabling them to provide accurate and reliable inspection results. The company’s professionals are trained in interpreting complex data and identifying even the most subtle flaws, ensuring the highest level of quality assessment.
Cutting-edge Technology and Equipment:
NDT & PWHT Solutions stands apart from competitors by utilizing state-of-the-art ECI technology and equipment. They regularly update their equipment to leverage the latest advancements in ECI technology, ensuring superior inspection accuracy and efficiency. By investing in advanced tools, they can effectively evaluate a wide range of materials, from thin coatings to thick-walled components.
Customized Solutions:
One of the key differentiators of NDT & PWHT Solutions is its ability to tailor ECI services to meet specific client requirements. The company understands that each industry and application may have unique needs and challenges. As a result, they offer customized inspection plans and methodologies, ensuring optimal detection of flaws and comprehensive evaluations. Their adaptability and flexibility in catering to diverse client needs contribute significantly to customer satisfaction.
Integrated Approach:
NDT & PWHT Solutions takes a holistic approach to ECI, offering a comprehensive suite of services that complement each other. They integrate ECI with other NDT techniques such as ultrasonic testing, radiography, and magnetic particle inspection to provide clients with a comprehensive evaluation of their assets. This integrated approach helps identify a broader range of defects and ensures a more accurate assessment of the material’s condition.
Exceptional Customer Service:
Customer satisfaction is at the core of NDT & PWHT Solutions’ philosophy. The company is known for its commitment to delivering high-quality services on time and within budget. They prioritize effective communication with clients, understanding their specific requirements, and offering prompt and reliable solutions. With a strong focus on building long-term relationships, they provide ongoing support, consultation, and guidance to help clients make informed decisions regarding asset integrity.
Conclusion:
Eddy Current Inspection is a crucial non-destructive testing technique that plays a vital role in maintaining the integrity and safety of materials and components. NDT & PWHT Solutions has established itself as a leader in providing ECI services, standing out from competitors through its expertise, advanced technology, customized solutions, integrated approach, and exceptional customer service. By continually striving for excellence, NDT & PWHT Solutions sets the benchmark for quality and reliability in the NDT industry, ensuring the satisfaction and trust of their clients.
Eddy Current Inspection (ECI) is a non-destructive testing (NDT) technique that has several benefits in the NDT industry. Here are some of the advantages of ECI:
Detects surface and near-surface defects: ECI is particularly effective in detecting surface and near-surface defects such as cracks, corrosion, pitting, and erosion. It can identify these flaws without the need for extensive surface preparation, making it a valuable tool for inspecting various materials and components.
Fast and efficient inspection: ECI is a rapid inspection technique that can quickly scan large areas and provide immediate results. It is especially useful in applications where time is a critical factor, such as in production lines or during periodic inspections.
Non-contact inspection: ECI is a non-contact method, meaning it does not require physical contact between the inspection probe and the test specimen. This feature allows for inspection of delicate or fragile materials without causing damage, preserving the integrity of the component being tested.
Suitable for conductive materials: ECI is primarily used for conductive materials, including metals and alloys. It can effectively detect defects in materials like aluminum, copper, steel, and titanium, making it a versatile technique in industries such as aerospace, automotive, and manufacturing.
High sensitivity: ECI is highly sensitive to small changes in conductivity, permeability, and geometry of the test material. This sensitivity enables it to detect minute defects, cracks, or variations in material properties that might not be visible to the naked eye.
Proximity and remote inspection capabilities: ECI can be employed for both proximity and remote inspections. Proximity inspection involves bringing the probe close to the test material, allowing for detailed examination of the surface. Remote inspection, on the other hand, enables the detection of defects through coatings or non-conductive materials.
Versatility in applications: ECI can be applied to a wide range of applications, including aircraft components, heat exchangers, pipes, welds, electrical conductors, and more. It can be used for quality control, in-service inspections, maintenance, and failure analysis, making it a valuable technique across various industries.
Real-time defect visualization: ECI systems often incorporate advanced imaging and display technologies, allowing inspectors to visualize and interpret inspection data in real-time. This capability facilitates quick decision-making and enhances the efficiency of the inspection process.
Overall, Eddy Current Inspection offers numerous benefits, including its ability to detect surface and near-surface defects, fast and efficient inspection, non-contact nature, suitability for conductive materials, high sensitivity, versatility, and real-time defect visualization. These advantages make ECI a valuable tool in the NDT industry for ensuring the quality, safety, and reliability of critical components and structures.
We Incorporate Computer-Based Test Instruments & Test Coils like Weld Inspection, Test Cut Length, wire & cable testing, real time.
For More Information Contact Our Expert Team: support@solutionss.org