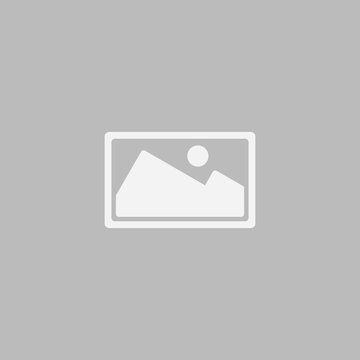
Wind Turbine Blade Inspection: Key NDT Techniques for Sustainable Energy
Introduction
As the demand for renewable energy grows, wind turbines play a crucial role in sustainable power generation. However, ensuring the structural integrity and long-term performance of wind turbine blades is critical to maintaining efficiency and safety. Non-Destructive Testing (NDT) techniques have become essential in detecting defects, preventing failures, and extending the service life of turbine components.
At NDT AND PWHT SOLUTIONS PVT LTD (India), we employ advanced NDT methodologies to enhance the reliability and sustainability of wind energy infrastructure. This article explores the key NDT techniques used in wind turbine blade inspections.
Common Defects in Wind Turbine Blades
Wind turbine blades are subject to harsh environmental conditions, including high winds, extreme temperatures, and mechanical stresses. Over time, these factors can lead to:
– Delamination in composite materials
– Cracks and fractures due to fatigue
– Erosion and corrosion from environmental exposure
– Bonding defects in adhesive joints
– Water ingress causing internal damage
Identifying these issues early through NDT ensures that corrective measures can be taken before catastrophic failures occur.
Key NDT Techniques for Wind Turbine Blade Inspection
1.Ultrasonic Testing (UT)
Ultrasonic testing is a highly effective method for detecting internal defects in composite wind turbine blades.
Benefits:
– Identifies delaminations and voids within fiber-reinforced structures
– Detects bonding defects in adhesive joints
– Provides quantitative measurements of material integrity
2.Acoustic Emission Testing (AET)
AET is a real-time monitoring technique that captures stress-induced acoustic signals to detect active defects.
Benefits:
– Early detection of structural issues
– Identifies areas prone to fatigue cracking
– Minimizes downtime by enabling in-service monitoring
3.Infrared Thermography (IRT)
Infrared thermography detects temperature variations that indicate subsurface defects.
Benefits:
– Non-contact inspection ideal for large blades
– Identifies delamination and moisture ingress
– Quick scanning enables rapid assessments
4.Digital Radiography (DR)
Digital radiography uses X-rays to inspect the internal structure of wind turbine blades.
Benefits:
– Detects hidden cracks and fiber misalignment
– High-resolution imaging for detailed defect analysis
– Applicable for both on-site and laboratory inspections
5.Visual Inspection with Drones
Drone-based visual inspection is a game-changer for inspecting hard-to-reach areas on wind turbine blades.
Benefits:
– Reduces the need for manual rope access
– Provides high-resolution imagery for defect analysis
– Cost-effective and improves inspection efficiency
The Future of NDT in Wind Energy
The integration of Artificial Intelligence (AI), automation, and digital twins is transforming wind turbine inspections. AI-driven NDT techniques can analyze large datasets, predict failure risks, and optimize maintenance schedules, ensuring maximum efficiency and longevity of wind energy assets.
Conclusion
NDT plays a pivotal role in ensuring the safety, reliability, and efficiency of wind turbine blades. At NDT AND PWHT SOLUTIONS PVT LTD (India), we leverage cutting-edge inspection technologies to support the global transition to sustainable energy solutions. With advanced ultrasonic testing, thermography, digital radiography, and drone-based inspections, we help wind energy operators maintain high-performance turbines while reducing downtime and maintenance costs.
By investing in innovative NDT solutions, the wind power industry can achieve greater sustainability, increased operational efficiency, and enhanced safety for years to come.