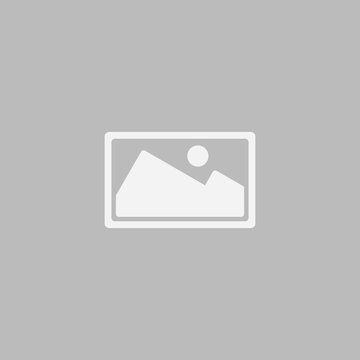
AI-Driven Predictive Maintenance: A Game-Changer for Industrial Inspections
Introduction
In today’s fast-paced industrial landscape, ensuring asset reliability and efficiency is more critical than ever. Artificial Intelligence (AI)-driven predictive maintenance is transforming the way industries conduct inspections, particularly in Non-Destructive Testing (NDT). By leveraging machine learning algorithms, real-time data analytics, and automation, industries can now detect anomalies, predict failures, and optimize maintenance schedules more effectively than traditional methods.
At NDT AND PWHT SOLUTIONS PVT LTD (India), we integrate cutting-edge AI-driven predictive maintenance solutions to enhance the safety, efficiency, and cost-effectiveness of industrial inspections across sectors such as oil & gas, aerospace, power generation, and heavy engineering.
The Shift from Reactive to Predictive Maintenance
Traditional maintenance strategies are typically classified into three categories:
– Reactive Maintenance: Addressing failures only after they occur, leading to costly downtime.
– Preventive Maintenance: Performing scheduled maintenance based on time or usage, which may lead to unnecessary servicing or missed failures.
– Predictive Maintenance: Using AI and machine learning to analyze real-time data, predict failures, and schedule maintenance only when necessary.
How AI-Driven Predictive Maintenance Works
AI-driven predictive maintenance utilizes a combination of technologies to improve NDT inspections:
1.Machine Learning and Data Analytics
Machine learning models analyze historical and real-time data from sensors and inspections to identify patterns that indicate potential failures. AI systems continuously learn and improve over time, enhancing prediction accuracy.
2.Internet of Things (IoT) Sensors
IoT-enabled sensors installed on industrial assets collect data on vibration, temperature, pressure, corrosion, and structural integrity. This data is transmitted to AI systems for real-time monitoring and early anomaly detection.
3.Automated Non-Destructive Testing (NDT)
AI-powered automated ultrasonic, radiographic, and thermographic inspections can analyze components without human intervention, reducing human error and increasing inspection speed.
4.Digital Twin Technology
A digital twin is a virtual replica of a physical asset. AI-driven predictive maintenance leverages digital twins to simulate and predict asset performance, enabling proactive decision-making.
5.Cloud-Based Predictive Analytics
Cloud-based platforms allow industries to store, analyze, and visualize inspection data, making it easier for maintenance teams to track asset health, generate reports, and optimize repair schedules remotely.
Benefits of AI-Driven Predictive Maintenance in NDT
– Reduced Downtime: Early detection of defects prevents unexpected failures, minimizing production losses.
– Lower Maintenance Costs: Maintenance is performed only when necessary, reducing unnecessary servicing expenses.
– Improved Safety: Identifying potential hazards before they escalate enhances workplace safety and regulatory compliance.
– Enhanced Asset Lifespan: Timely interventions prevent excessive wear and tear, extending asset longevity.
– Higher Inspection Accuracy: AI algorithms reduce human errors in defect detection and interpretation.
Industries Benefiting from AI-Driven Predictive Maintenance
1.Oil & Gas
– Pipeline integrity monitoring and leak detection
– Offshore rig structural inspections
2.Aerospace
– Aircraft engine and fuselage monitoring
– Composite material integrity assessments
3.Power Generation
– Predictive turbine and boiler maintenance
– Nuclear plant safety monitoring
4.Heavy Engineering & Manufacturing
– Structural health monitoring of critical machinery
– Weld integrity assessment in large-scale production
Future of AI in Predictive Maintenance
The future of AI-driven predictive maintenance is evolving rapidly, with innovations such as:
– AI-Powered Autonomous Inspection Drones: Performing real-time inspections in hazardous environments.
– Edge Computing for Faster Data Processing: Enhancing real-time decision-making without cloud dependency.
– Advanced AI Algorithms for Root Cause Analysis: Pinpointing the exact cause of failures for precise corrective actions.
Conclusion
AI-driven predictive maintenance is revolutionizing Non-Destructive Testing (NDT) and industrial inspections by providing real-time monitoring, accurate defect detection, and proactive maintenance strategies. At NDT AND PWHT SOLUTIONS PVT LTD (India), we are at the forefront of implementing AI-driven solutions to ensure maximum asset reliability and operational efficiency.
By embracing AI-powered predictive maintenance, industries can achieve cost savings, enhanced safety, and improved performance, paving the way for a smarter and more efficient future in industrial inspections.