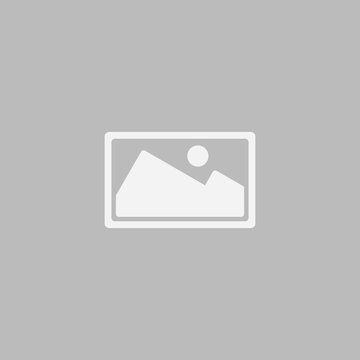
Introduction to Non-Destructive Testing (NDT): Methods and Applications
Introduction
Non-Destructive Testing (NDT) plays a vital role in ensuring the safety, reliability, and longevity of industrial components across various industries. By allowing for the inspection and evaluation of materials without causing damage, NDT helps in identifying defects and inconsistencies before they lead to critical failures.
At NDT AND PWHT SOLUTIONS PVT LTD (India), we specialize in cutting-edge NDT techniques that cater to industries such as oil & gas, aerospace, marine, power generation, and infrastructure. This article explores the fundamentals of NDT, the different testing methods, and their applications.
What is Non-Destructive Testing (NDT)?
Non-Destructive Testing (NDT) refers to a range of inspection techniques used to evaluate the properties of a material, component, or system without causing damage. These methods help detect flaws, cracks, corrosion, and material inconsistencies while maintaining the integrity of the tested item.
Key Benefits of NDT:
– Ensures safety and reliability in critical components
– Reduces downtime and maintenance costs
– Enhances quality control and compliance with industry standards
– Prevents catastrophic failures in infrastructure and equipment
Common NDT Methods and Their Applications
1.Visual Testing (VT)
– Principle: Involves direct or remote visual inspection of a component using the naked eye or optical instruments.
– Applications:
– Surface crack detection in welds and pipelines
– Corrosion assessment in industrial structures
– Inspection of aircraft fuselages and ship hulls
2.Ultrasonic Testing (UT)
– Principle: Uses high-frequency sound waves to detect internal flaws in materials.
– Applications:
– Weld integrity testing in pipelines and pressure vessels
– Thickness measurements in corrosion monitoring
– Detection of hidden defects in aerospace components
3.Radiographic Testing (RT)
– Principle: Uses X-rays or gamma rays to produce an image of internal structures.
– Applications:
– Detecting weld defects in pressure vessels
– Inspecting composite materials in aerospace
– Pipeline integrity assessment
4.Magnetic Particle Testing (MPT)
– Principle: Utilizes magnetic fields and ferromagnetic particles to detect surface and near-surface flaws.
– Applications:
– Detecting cracks in ferrous components
– Weld inspections in bridges and offshore structures
– Assessing fatigue cracks in railway tracks
5.Liquid Penetrant Testing (LPT)
– Principle: Applies a liquid dye that seeps into surface cracks, which is then made visible under ultraviolet or visible light.
– Applications:
– Detecting surface flaws in non-porous materials
– Aerospace and automotive component inspections
– Inspection of castings and forgings
6.Eddy Current Testing (ECT)
– Principle: Uses electromagnetic induction to detect surface and near-surface defects in conductive materials.
– Applications:
– Inspecting heat exchanger tubes
– Crack detection in aircraft structures
– Corrosion detection in pipelines
7.Phased Array Ultrasonic Testing (PAUT)
– Principle: An advanced form of UT that uses multiple ultrasonic beams for improved imaging.
– Applications:
– High-precision weld inspections
– Complex component analysis in aerospace
– Advanced corrosion mapping in oil & gas pipelines
8.Time of Flight Diffraction (TOFD)
– Principle: Uses ultrasonic waves and time delay analysis to detect and size flaws.
– Applications:
– High-accuracy crack sizing in welds
– Pipeline and refinery inspection
– Structural integrity assessment in power plants
Industries Benefiting from NDT
1.Oil & Gas
– Pipeline corrosion and weld integrity assessment
– Pressure vessel and storage tank inspections
2.Aerospace
– Aircraft fuselage and composite material testing
– Engine component fatigue analysis
3.Power Generation
– Turbine blade and boiler tube inspections
– Nuclear reactor weld evaluations
4.Marine & Offshore
– Ship hull integrity assessment
– Offshore structure fatigue monitoring
5.Infrastructure & Construction
– Bridge and highway structural inspections
– High-rise building safety assessments
Conclusion
Non-Destructive Testing (NDT) is an essential component of modern industrial safety and quality assurance. At NDT AND PWHT SOLUTIONS PVT LTD (India), we provide state-of-the-art NDT solutions tailored to meet the stringent requirements of various industries. Our advanced methodologies ensure precision, reliability, and compliance with international standards, helping businesses maintain their assets safely and efficiently.
With continuous advancements in AI, robotics, and automation, NDT is set to revolutionize inspection methodologies, making industries safer and more cost-effective. Contact us today to learn how our comprehensive NDT services can benefit your operations!